Maximizing Efficiency with the Right Machinery for Your Production
- avinyaesemplast
- Dec 3, 2024
- 4 min read
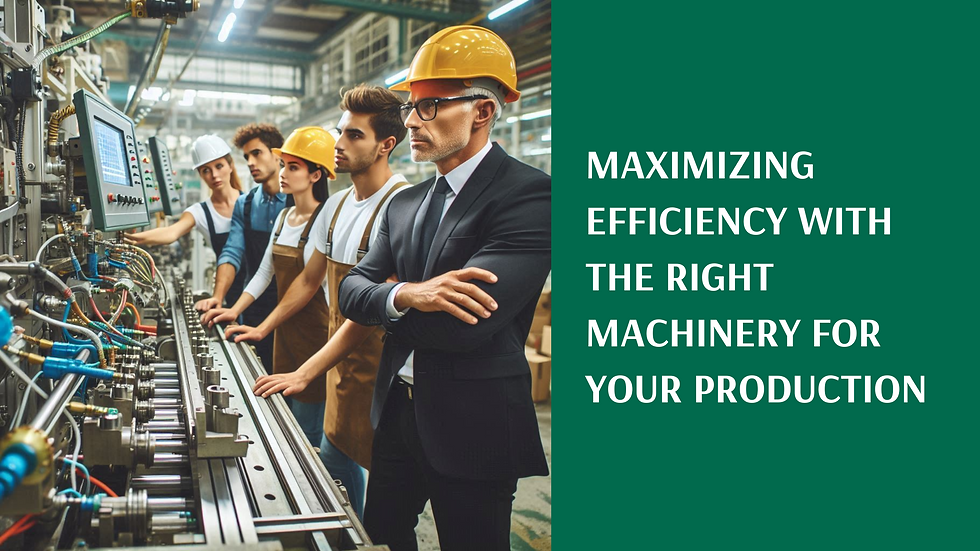
Maintaining an advantage in the highly competitive manufacturing sector requires optimizing production efficiency. One of the most crucial aspects of achieving this goal is selecting the right equipment for your production process. Bottles, containers, and other intricate shapes are made from hollow plastic using a technique that calls for accuracy and top-notch equipment. Choosing the right equipment is vital to ensuring quality products while minimizing downtime. This article explores how the right machinery can maximize efficiency in your production, with a particular focus on working with reliable injection blow moulding machine manufacturers.
Understanding the Production Process
Production processes for creating hollow plastic products vary, with different techniques offering unique advantages. The methods of extrusion, injection blow forming, and stretch forming all serve specific needs, but the choice of technique depends on the desired product, material, and production requirements.
Among these, the injection blow forming process has gained popularity due to its precision and ability to produce high-quality products with uniformity. The process involves injecting molten plastic into a preformed shape, then applying air to achieve the final product shape. The result is a part that is stronger, more durable, and has greater dimensional accuracy than products made using other techniques.
How the Right Equipment Impacts Efficiency
Choosing the appropriate equipment for your needs plays a key role in optimizing efficiency. The right tools influence various aspects of the production process, from product quality and cycle times to material use and overall speed. Here’s how selecting the best technology impacts efficiency
1. Precision and Consistency
One of the key advantages of using the right equipment is the precision it offers. With advanced technology, manufacturers can achieve high-quality parts with tight tolerances and consistent shapes, reducing waste and rework. The latest machines are designed to maintain tight control over every part of the production process, from the initial injection phase to the final shaping process. This control ensures that parts meet design and performance standards every time.
2. Faster Production Cycles
Speed is crucial to enhancing manufacturing efficiency. The right equipment can dramatically improve production rates without compromising on the quality of the finished product. Modern machinery boasts faster cycle times, which are enhanced by automation and efficient material handling systems. Some equipment even incorporates multi-cavity moulds, allowing manufacturers to produce multiple parts simultaneously. This efficiency boosts throughput, helping companies meet larger production targets in less time.
3. Energy Efficiency
Energy consumption is one of the largest operational costs for manufacturers. To keep costs low, it is crucial to choose energy-efficient equipment. Many new models incorporate energy-saving technologies, such as optimized heating systems, variable-speed drives, and advanced cooling processes. By investing in these energy-efficient solutions, manufacturers can reduce both their operating expenses and environmental impact, making sustainability a key consideration.
4. Reduced Downtime
Reducing downtime is essential to maintaining consistent output levels. Whether caused by equipment failure, maintenance issues, or other challenges, unplanned downtime can lead to delays and increased costs. The risk of such problems can be minimized by choosing equipment from reputable injection blow molding manufacturers. Modern systems are equipped with diagnostic tools that detect potential issues early, helping operators maintain smooth operations. Furthermore, many of these systems have easily replaceable components, enabling faster repairs, reducing downtime, and maximizing production efficiency.
5. Optimized Material Usage
Minimizing material waste is another area where efficiency can be improved. High-quality equipment ensures that the amount of plastic used in each cycle is precise, preventing overuse and material waste. Advanced machines also offer versatility, capable of handling a variety of materials, giving manufacturers the flexibility to select the most cost-effective and suitable material for each product. Optimizing the use of materials lowers operating expenses and boosts overall production effectiveness.
The Value of Selecting the Correct Equipment Supplier
While selecting the appropriate machinery is essential for improving efficiency, partnering with experienced and reliable equipment providers is equally important. The likelihood of such problems can be decreased by selecting tools from trusted injection blow molding equipment suppliers.
These experienced providers not only offer top-of-the-line machinery but also provide valuable expertise and ongoing support. They understand the diverse needs of various industries and can recommend the right equipment for your production line. Whether you need equipment for large-scale production or more complex moulding tasks, they can guide you in making the best decision.
Moreover, established manufacturers offer comprehensive after-sales services, including training, maintenance, and troubleshooting support. This continuous assistance is crucial for keeping your equipment in optimal working condition and preventing costly production interruptions.
Conclusion
Maximizing efficiency with the right equipment is crucial for any manufacturer looking to stay competitive in today’s market. Whether you're aiming to improve precision, speed, energy efficiency, or material usage, the right machinery can have a significant impact on production. When selecting equipment, partnering with trusted injection blow moulding machine manufacturers ensures that you’re not only investing in the best technology but also receiving the necessary support to keep your operation running smoothly. With the right machinery and a reliable supplier, your production efficiency will thrive, ultimately leading to greater profitability and success in the manufacturing world.
Comments