Examining the Most Recent Developments in Injection Molding Technology for Plastic
- avinyaesemplast
- Dec 19, 2024
- 4 min read
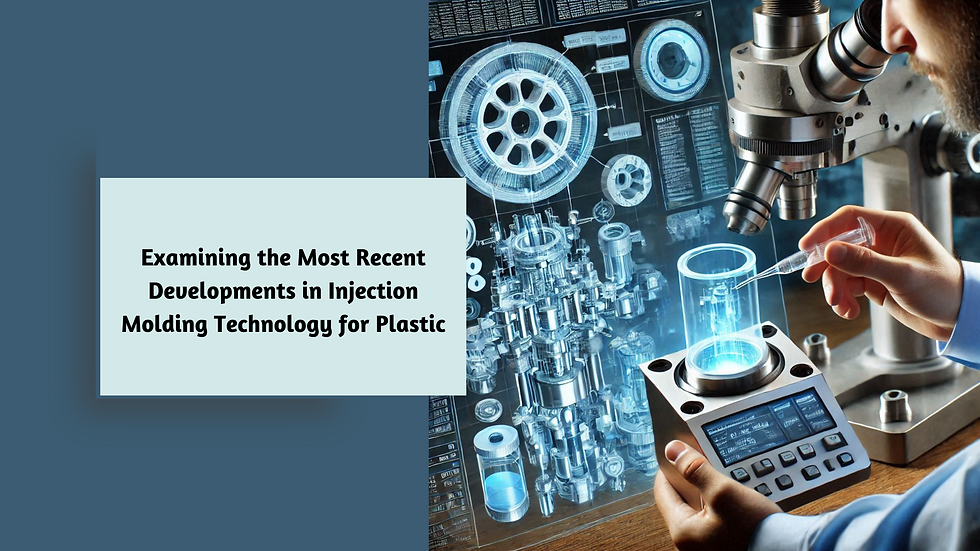
The global manufacturing sector has always been fueled by technological advancements, and the production of moulded components is no exception. This versatile process has evolved considerably over the years, with significant contributions from plastic injection moulding machine manufacturers in India, who continue to push the boundaries of innovation. In this article, we’ll delve into the recent advancements that are shaping the future of this essential manufacturing technique.
The Evolution of Moulding Technology
Moulding involves injecting molten material into a specific form, creating intricate and complex designs. This method has come a long way, evolving from manual techniques to automated systems powered by sophisticated technology. Today, these systems offer greater efficiency, precision, and environmental responsibility compared to their predecessors.
Innovations Shaping the Industry
Several key innovations have emerged, with major developments coming from plastic injection moulding machine manufacturers in India. Let’s explore these breakthroughs:
1. Energy Efficiency and Sustainability
The push toward more energy-efficient production methods is one of the most prominent trends. With rising concerns about energy consumption and sustainability, new technologies focus on reducing power usage while maintaining high performance. The introduction of advanced hydraulic systems and servo motors has led to machines that consume significantly less energy.
Benefits of These Innovations:
Reduced power usage
Lower operational costs
Environmentally friendly
This shift towards greener production techniques helps companies lower their carbon footprint, making them a more attractive choice for industries aiming to meet environmental goals.
2. Automation and Smart Manufacturing
Automation has long been a key component of the manufacturing process, but recent developments have taken automation to the next level. With the incorporation of Internet of Things (IoT) sensors,AI-driven software, and real-time monitoring capabilities, manufacturers can now enjoy enhanced efficiency, reduced downtime, and faster production cycles.
Smart Features Include:
Predictive maintenance and real-time diagnostics
Remote monitoring
Automated quality checks
Data-driven production optimization
These innovations enable manufacturers to fine-tune operations in real time, ensuring maximum efficiency and minimal errors. Leading companies in India are adopting Industry 4.0 technologies, making production smarter and more integrated.
3. High Precision and Complex Component Production
As industries demand increasingly intricate and precise components, advancements in technology have made it easier to produce these complex parts. Features like multi-material injection, which allows for the integration of various substances in one cycle, and micro-injection systems for producing miniature parts have enhanced the versatility of the moulding process.
Advanced systems allow the creation of hybrid components combining plastics, metals, or other materials, which are essential for the automotive, electronics, and medical device sectors. Micro-injection moulding also ensures the production of high-precision components for devices that require extremely small parts, such as in electronics or medical devices.
4. Faster Production and Reduced Cycle Time
Another breakthrough is the reduction of cycle times, which boosts productivity. Manufacturers are using advanced cooling technologies, faster injection systems, and optimized temperature controls to speed up the process while ensuring high-quality outputs.
By shortening cycle times, production volumes increase, and costs are reduced, which is essential for businesses looking to stay competitive. These innovations are particularly valuable for mass production, allowing manufacturers to meet growing market demands without sacrificing quality.
5. Material Compatibility and Eco-Friendly Alternatives
The ability to work with a wide range of materials is another key advancement. Today’s systems are designed to handle biodegradable plastics, recycled materials, and composites, enabling manufacturers to produce eco-friendly products without compromising on strength or durability.
This is particularly important in industries such as packaging, automotive, and consumer goods, where sustainability is a growing concern. Using recycled plastics and alternative materials not only helps reduce environmental impact but also meets the increasing demand for green products.
6. Enhanced Operator Interfaces
Modern systems now feature sophisticated yet user-friendly control interfaces. Touchscreen panels, customizable dashboards, and intuitive software make machine operation easier and more efficient. These systems allow for real-time adjustments and performance tracking, improving overall operational control.
Additionally, automation features like parameter optimization and mold wear monitoring make it easier to maintain consistent quality throughout production. These controls reduce human error and streamline processes, leading to more reliable outputs.
The Future of Moulding Technology
The future of this technology looks promising, with more innovations on the horizon. As artificial intelligence, robotics, and advanced analytics continue to develop, the process of moulding is set to become even more self-sufficient and efficient. The incorporation of new materials and the further drive towards sustainability will likely shape the industry, as manufacturers strive to create environmentally friendly yet high-performance products.
As these innovations continue to evolve, plastic injection moulding machine manufacturers in India will remain at the forefront of the industry, driving global standards. With a focus on efficiency, sustainability, and precision, the future of moulding technology is bright, offering limitless opportunities for manufacturers and industries worldwide.
Conclusion
Innovations in moulding technology are revolutionizing the way products are manufactured, offering faster, more energy-efficient processes that meet the evolving demands of global industries. From enhanced precision to eco-friendly solutions, the latest advancements from plastic injection moulding machine manufacturers in India ensure that the industry continues to thrive. These innovations not only make the production process more efficient but also open the door for more sustainable and cost-effective manufacturing solutions, ensuring a competitive edge in the marketplace.
Comments